The innovative conception of Atom Smart Press owes its strength to the fully integrated process of design, manufacturing, assembling and test that characterizes Atom group in the world. Atom conceives and manufactures the whole system: from hydraulics, to mechanics, to electronics, to software. Atom engineers have designed all of these machines. Accordingly, operating software have been designed simultaneously for absolute compatibility and full integration.
Relco Roller Press: Easy operation
No special skills are required to operate the cutting press. Your current cutting press operators can use it. Machine programming and nesting may be carried out either locally or remotely from your production planning office. Cutting programs can be transferred through network or diskette. The work schedule automatically controls the press and tells the operators when to change materials and tools. Additionally, if your material width varies, or if rush jobs require immediate priority, the operator can instantly re-nest the schedule to accommodate this. Furthermore, standard cutting tools are fitted onto a simple steel carrier plate and are easily replaceable on the cutting head in less than 10 seconds.
Strong construction
These cutting presses are pure CNC machines, not manual presses retro-fitted with some automatic features. The construction of the presses, designed on the latest CAD systems, is the most robust and rigid available.
Simple belt change
This unique feature reduces downtime and allows for complete in-house maintenance.
Unrivaled Algorithms
The nesting software gives the best material utilization and fastest cutting speeds available.
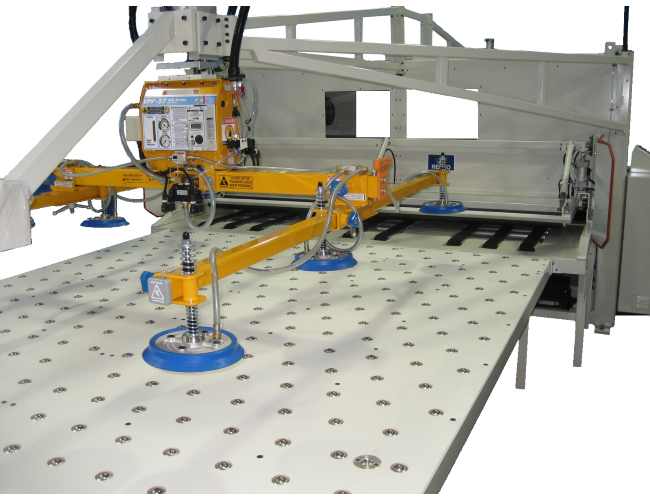